“We could not have launched this life-saving product line without the support of 3D Printing Tech. Their critical knowledge of material properties and processes, combined with their ability to lay out a future cost structure of fulfillment in the early stages of prototyping allowed us to gain an early understanding of the feasibility of the product’s ROI.”
Product Managerat HELLA Automotive, Michael Sobotka
BACKGROUND
The dream for HELLA was born in 1899 in Lippstadt, Germany.At the time, they specialized in building lanterns, headlamps, horns, and fittings for bicycles, carriages, and automobiles. They have now grown to a global company with over 125 locations in 35 different countries. The organization develops and manufactures lighting and electronic components as well as systems for automobiles. With sales of $7.3 billion in the fiscal year 2020/2021 and 36,000 employees, HELLA is one of the leading automotive suppliers.
CHALLENGE
HELLA Automotive has been developing, refining, and manufacturing vehicle lighting for over 100 years.
Recently, they began developing an LED headlamp replacement for police and emergency vehicles, and identified two problems with existing replacements that were on the market:
1) The warning lights (turn signals, brake lights, etc.) on emergency vehicles do not function when the flashing lights are enabled. This is an obvious problem for police departments as it can create unsafe driving conditions and can lead to accidents.
2) The procedures for installing the alternative headlamp can lead to costly mistakes for the installers, such as drilling errors and poor silicone seals that can damage the vehicle. Long curing times for the epoxy used to lock bezels in place also slows the overall process.
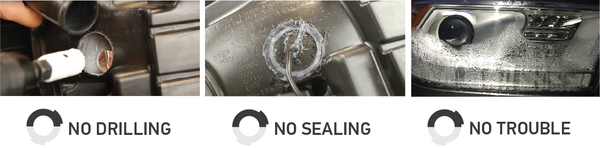
STAKEHOLDERS
1) HELLA Automotive – Needed a profitable product to add to their portfolio
2) Installation Teams – Needed an improved method for installing headlamp upgrades to reduce time and costly damage
3) Police Departments/First Responders –Needed improved safety in their vehicle fleet
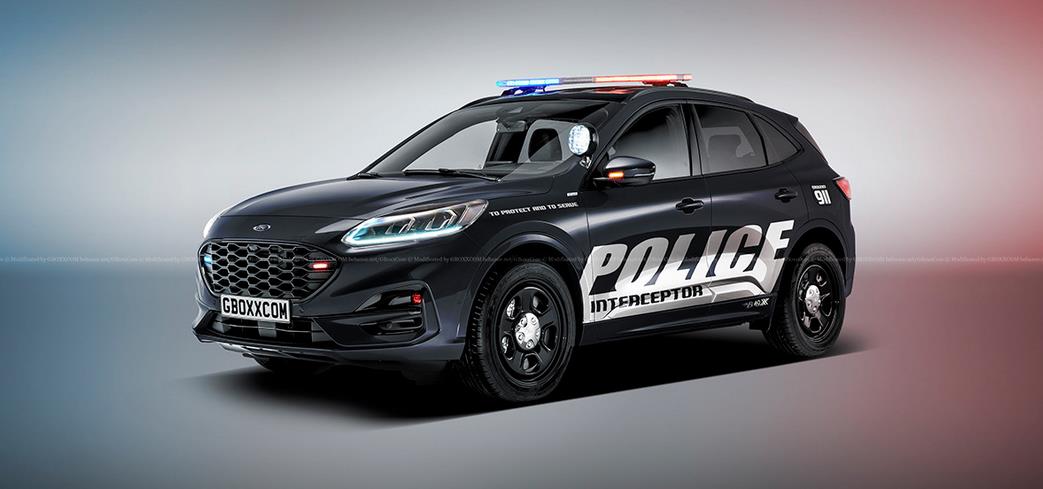
HELLA’S STARTING POINT TO FIND A SOLUTION
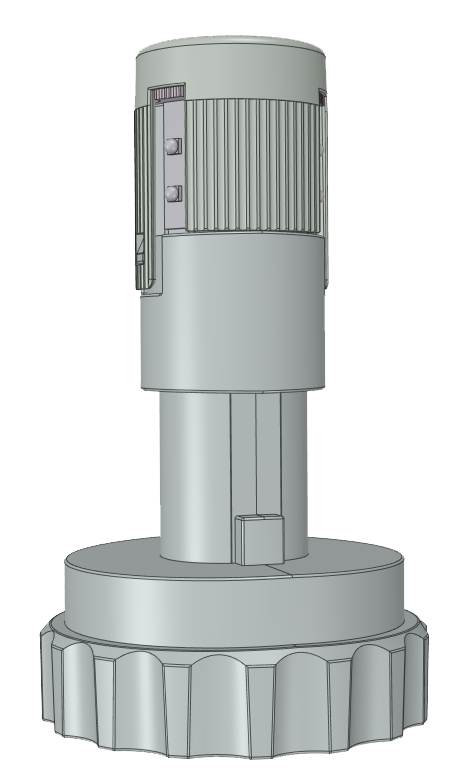
HELLA understood that they had several roadblocks in front of them to fill the needs of the stakeholders involved.
The first was how to develop a product that could be easily installed into the variety of existing mounts across the different makes, models, andyears of vehicles.
After iterating on a few ideas, they landed on a modification to the cylindrical body to fit a collar that includes two semi-circle pieces that snap together and are shaped to match the headlamp shape of the vehicle into which they were installed.
HELLA believed that they had found a solution but knew they would need to prototype first and then produce a large variety of adaptors in small batches. This meant traditional manufacturing methods like injection molding were not viable options.
In addition, HELLA understood that they had to find a material that had higher temperature resistance due to the operating conditions. At that stage they reached out to 3D Printing Tech to determine if 3D printing was a solution.
3D PRINTING TECH’S PROCESS ENABLES HELLA TO ADDRESS STAKEHOLDERS’ NEEDS
Ultimately, HELLA needed a profitable product to add to their portfolio that installers could use and was made of the right material to withstand its customers’ operating conditions.
Profitable Product
The team at 3D Printing Tech provided reliable final production run cost estimates to HELLA at the start, which allowed HELLA to validate ROI in the early stages. Understanding the costs involved gave HELLA confidence to move forward with the research and development for the project.
Right Material
Once the ROI was validated, 3D Printing Tech assisted with material testing and selection. At first, FDM/FFF printing was tested with a variety of filaments such as ABS, PETG, PolyMide from PolyMaker, and Alfa+ from FiloAlfa. The filament that could provide the best finish and performance in the high temperature environment was Alfa+.
Although this was a viable material that HELLA approved, a filament-based product did not live up to the expectations of the installers who were not used to seeing 3D-printed parts. In addition, producing quantities of FDM/FFF parts in an exotic material posed a challenge to quality control for 3D Printing Tech.
At this stage, 3D Printing Tech moved on to testing SLS as a production method using Nylon12 powder sintered with the MfgPro230 xS from XYZPrinting. This 3D printing method proved to be the best solution for a final product.
The parts were printed in the natural white color of the Nylon12 powder and then went through a dying procedure resulting in black parts to match the color specified by HELLA.
Usable by Installers
The final parts also matched the look of traditionally manufactured parts and therefore were well received by the installation teams.
Operational for Customers
With the black Nylon12 powder sintered, semi-circle pieces were easily installed to match the headlamp shape for each vehicle. First responders could now use their warning lights when flashing lights were enabled.
Added Certainty
In addition, 3D Printing Tech’s use of SLS allowed it to produce over 1000 parts per SLS build – always providing the ability to produce enough parts fast enough to keep up with HELLA’s needs.
CONCLUSION
HELLA, along with 3D Printing Tech’s assistance, was able to quickly prototype and manufacture a product that met the needs of all the stakeholders involved.
1) HELLA had a profitable, stand-alone product that allowed them to increase market share.
2) Installers had a product that looked and felt like a traditionally manufactured item that is both easy and fast to install. This brought their costs down and increased their revenue.
3) The warning lights on the Police Departments’ and First Responders’ vehicles could function when the flashing lights were enabled. This created safer driving conditions and led to reduced accidents and costs.
3D PRINTING TECH COMPANY OVERVIEW
3D Printing Tech specializes in production quantity and large-volume 3D printing with laser sintering (SLS) and filament extrusion (FDM/FFF) methods. Its customers include fast-growing, mid-sized, large, and Fortune 500 companies. In addition to 3D printing, 3D Printing Tech utilizes 3D modeling/scanning, laser cutting, and vacuum forming to support its production and client projects. The team’s understanding of the importance of effective communication, and its commitment to helping people understand how to use 3D printing to grow their businesses and create efficiencies in manufacturing and production, are foundational to the long-term relationships it forms.